Premier Metal Fabricators at DeepMould.net: Specializing in Injection Molded Plastic for Diverse Industries
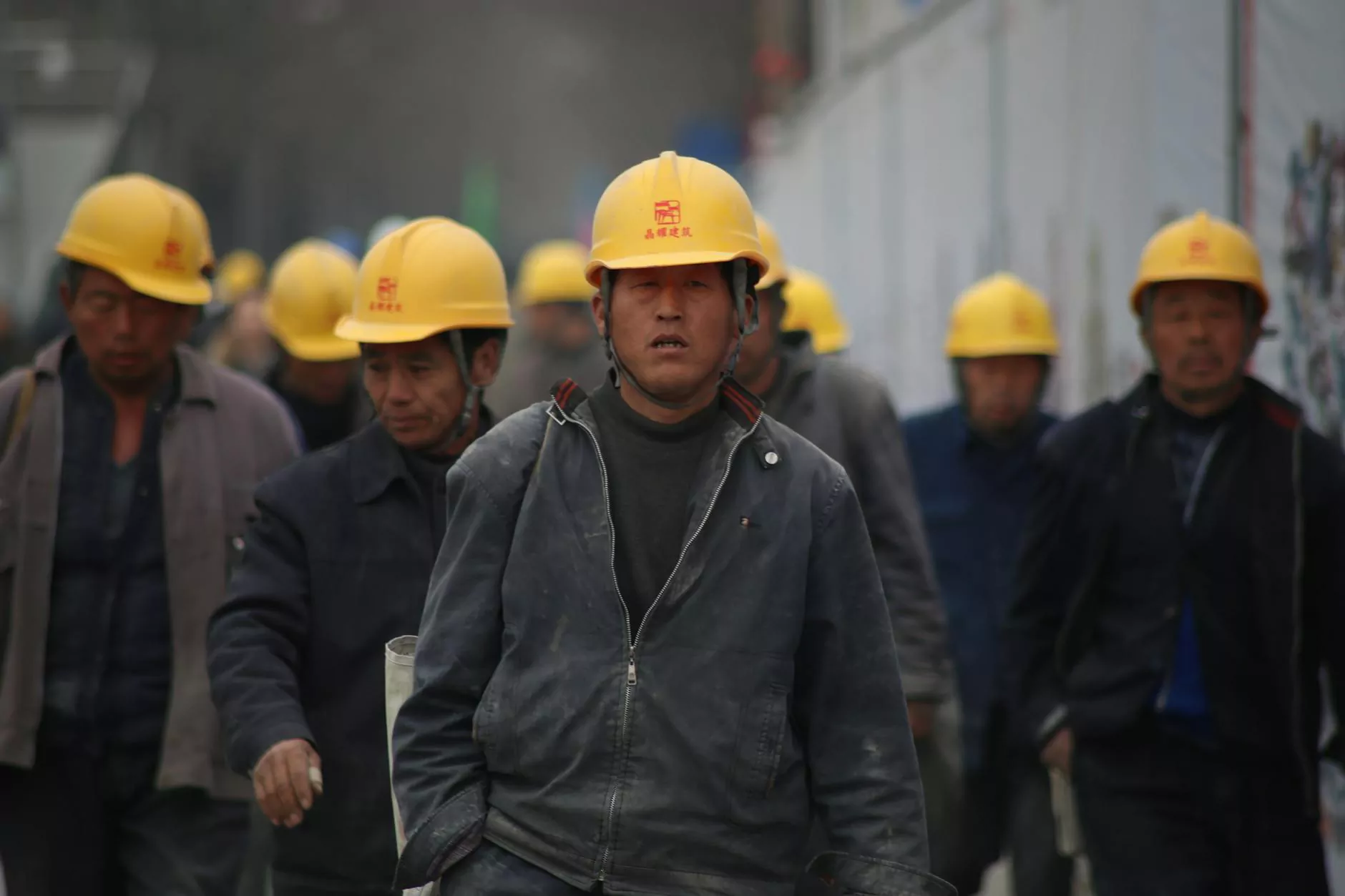
In the highly competitive world of modern manufacturing, the demand for precision, quality, and innovation has never been greater. At DeepMould.net, our team of expert metal fabricators are committed to providing top-tier services that meet the evolving needs of industries ranging from automotive to consumer electronics. Our specialization in injection molded plastic components sets us apart as leaders in integrating metal fabrication with advanced plastic molding techniques to deliver comprehensive solutions for our clients.
Why Choose DeepMould.net for Your Metal Fabrication and Plastic Injection Needs?
- Decades of Expertise: Our team brings extensive experience in metal fabrication, ensuring every project meets the highest standards of quality and precision.
- Advanced Technology: We utilize cutting-edge equipment and innovative manufacturing processes, including automation and quality management systems, to produce superior components.
- Integrated Solutions: Our ability to combine metal fabrication with injection molded plastic components offers clients a seamless, one-stop-shop experience.
- Quality Assurance: Rigorous inspection protocols and adherence to international standards guarantee durable, reliable products.
- Customer-Centric Approach: Customized solutions tailored to your unique specifications, timelines, and budgets.
Understanding the Role of Metal Fabricators in Modern Manufacturing
Metal fabricators form the backbone of manufacturing, transforming raw materials into precise components that serve as the foundation for numerous products. Our metal fabrication services encompass a variety of techniques, such as cutting, welding, bending, and finishing, allowing us to create complex geometries and durable structures needed across various sectors.
The Importance of Precision in Metal Fabrication
Precision is paramount in metal fabrication, especially when integrating with other manufacturing processes like injection molded plastic. Our advanced CNC machining and laser cutting technologies enable us to achieve micron-level accuracy, ensuring tight tolerances and perfect fitment of assembled parts. This precision translates into enhanced product performance, longevity, and customer satisfaction.
Injection Molded Plastic: An Industry Game-Changer
The use of injection molded plastic has revolutionized product design and manufacturing, offering unparalleled advantages in terms of production speed, cost-efficiency, and design flexibility. From tiny electronic components to large consumer appliances, injection molding enables the mass production of complex shapes with high repeatability.
Advantages of Injection Molded Plastic Components
- Cost-effective Production: Once the mold is created, manufacturing high volumes becomes economical, reducing overall costs per unit.
- Design Versatility: Intricately detailed and complex geometries can be achieved without additional tooling costs.
- High Reproducibility: Consistent quality across millions of parts ensures reliability and brand integrity.
- Material Diversity: A broad range of plastics, including ABS, polycarbonate, nylon, and more, are available for different application needs.
Synergy of Metal Fabrication and Injection Molded Plastic in Manufacturing
The integration of metal fabrication with injection molded plastic components creates multifunctional products with superior strength, durability, and aesthetic appeal. This synergy allows manufacturers to optimize designs, reduce assembly complexity, and enhance overall product performance.
Applications of Combined Metal and Plastic Manufacturing
- Electronics Housing: Metal frames provide structural integrity, while plastic covers offer lightweight protection and design flexibility.
- Automotive Components: Metal chassis parts combined with plastic trim and interior components for weight reduction and cost savings.
- Medical Devices: Durable metal bases coupled with precision-molded plastic housings for safety and ease of sterilization.
- Consumer Products: Instruments, appliances, and gadgets benefit from the combination of strength and aesthetic versatility.
Our Manufacturing Process: From Concept to Completion
1. Design and Prototype Development
We collaborate closely with clients to develop detailed CAD models, ensuring that design specifications are optimized for both metal fabrication and plastic injection molding. Rapid prototyping services allow for functional testing and iterative improvements before mass production.
2. Tooling and Mold Fabrication
Our skilled technicians create precise molds using high-grade steel and advanced machining techniques. This step is critical to achieving the tight tolerances and intricate designs required for complex assemblies.
3. Metal Fabrication
Using CNC machining, laser cutting, welding, and finishing, we produce metal parts according to specifications. These components undergo meticulous quality checks to verify dimensions, strength, and surface quality.
4. Injection Molding of Plastic Components
Our state-of-the-art injection molding machines produce high volumes of plastic parts with consistent quality. We select materials based on performance, environmental exposure, and cost considerations.
5. Assembly and Quality Control
Final assembly combines metal and plastic parts, followed by rigorous testing to ensure each product meets or exceeds industry standards. Inspection protocols include visual examination, dimensional verification, and functionality testing.
Why Quality Assurance Is Vital in Metal Fabrication and Injection Molding
Ensuring the highest quality in manufacturing is essential for building trust and long-term success. At DeepMould.net, we implement comprehensive quality assurance measures, including ISO standards compliance, real-time monitoring, and detailed documentation. Our goal is to deliver products that are not only precise but also durable, reliable, and aesthetically appealing.
Innovative Solutions and Future Trends in Metal Fabrication and Plastic Injection Molding
The manufacturing industry is continually evolving, driven by technological advancements and changing market demands. Some of the emerging trends include:
- Smart Manufacturing: Integration of IoT and automation to enhance process control and reduce waste.
- Advanced Materials: Development of high-performance plastics, composites, and biodegradable options.
- 3D Printing: Rapid prototyping and small-batch production, complementing traditional methods.
- Sustainable Practices: Recycling, energy-efficient processes, and eco-friendly materials to reduce environmental impact.
At DeepMould.net, we are committed to staying at the forefront of these trends, continually investing in new technologies and methodologies. Our focus on innovation ensures that clients benefit from cutting-edge solutions tailored to meet current and future market needs.
Partnering with DeepMould.net for Your Manufacturing Needs
Whether you require complex injection molded plastic parts, precision metal components, or integrated assemblies, we are your trusted partner. Our team is dedicated to providing personalized service, technical expertise, and unmatched quality to help your business succeed.
Contact us today to discuss your project requirements and discover how our comprehensive manufacturing solutions can drive your productivity and competitiveness to new heights.
Conclusion
In a world where product quality, innovation, and efficiency determine success, partnering with a proficient metal fabricator like DeepMould.net offers invaluable advantages. Our mastery over metal fabrication combined with mastery in injection molded plastic components empowers us to deliver comprehensive solutions tailored to the most demanding specifications.
Embrace the future of manufacturing with DeepMould.net — your reliable source for integrated metal and plastic fabrication services that unlock endless possibilities for your products and your business growth.