Thermoforming Mold Design: Unlocking the Future of Product Design
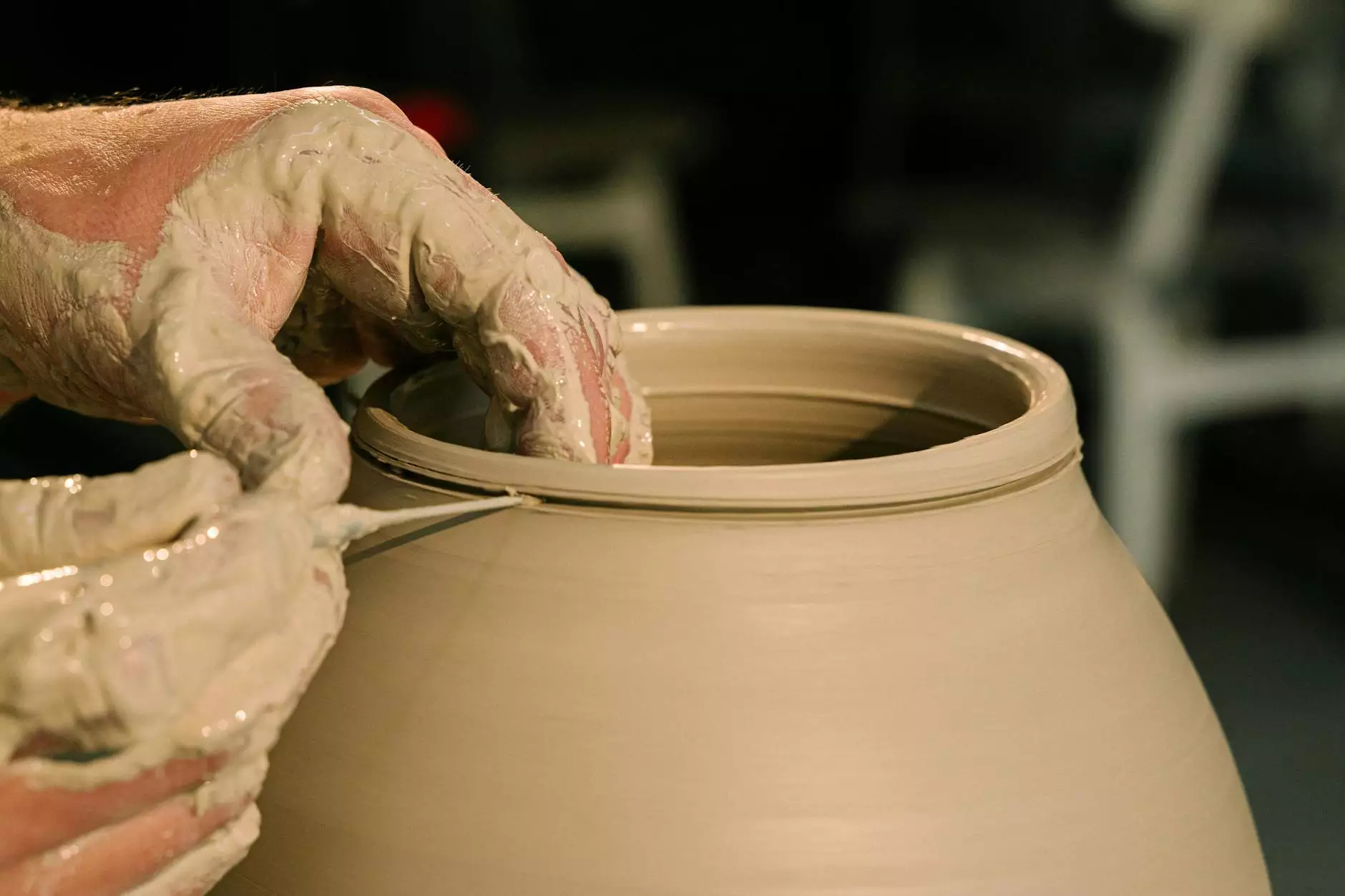
In today’s rapidly evolving manufacturing landscape, thermoforming mold design has emerged as a cornerstone of innovation and efficiency. This sophisticated process not only enhances product versatility but also accommodates the dynamic demands of various industries, including packaging, automotive, and consumer goods. In this in-depth article, we delve into the fundamentals of thermoforming mold design, explore its numerous applications, and examine how it seamlessly integrates with modern advancements in 3D printing and product design.
Understanding Thermoforming Mold Design
At its core, thermoforming is a manufacturing process that involves heating a plastic sheet until it becomes pliable and then forming it over a mold to create a specific shape. The thermoforming mold design is critical, as it dictates the quality, precision, and functionality of the final product. This process can either be vacuum forming, pressure forming, or a combination of both, each possessing distinct advantages depending on the application.
The Thermoforming Process Explained
- Heating: The first step in the thermoforming process involves heating a thermoplastic sheet to a temperature that allows it to be manipulated without breaking.
- Forming: Once heated, the plastic sheet is draped over the mold and either vacuum or pressure is applied to form the material against the mold’s contours.
- Cooling: The formed plastic is then cooled to harden it, after which it retains the mold's shape.
- Trimming: Finally, any excess material is trimmed away to prepare the finished product for further processing.
Benefits of Effective Thermoforming Mold Design
The design of thermoforming molds plays a pivotal role in achieving optimal results in various aspects, such as cost, material efficiency, and product quality. Here are some notable benefits:
- Cost-Effective Production: By optimizing mold design, manufacturers can significantly reduce material waste and production time, leading to lower overall costs.
- Enhanced Product Quality: A well-designed mold results in better dimensional accuracy and surface finish, enhancing the overall quality of the final product.
- Versatility: Thermoforming allows for a wide range of designs and shapes, providing manufacturers with the flexibility to meet diverse customer needs.
- Speed of Production: Advanced thermoforming processes enable rapid production cycles, which is crucial for businesses that need to respond quickly to market changes.
Applications of Thermoforming Mold Design
Thermoforming mold design finds relevance across various sectors, showcasing its adaptability and effectiveness. Here are some of its key applications:
1. Packaging Industry
The packaging industry has extensively adopted thermoforming due to its ability to produce lightweight yet sturdy containers. Products can be packaged efficiently, ensuring the preservation of quality while minimizing material use.
2. Automotive Sector
Within the automotive industry, thermoforming is used to create both interior and exterior components. This includes dashboard elements, panels, and protective coverings, all of which benefit from customized molds designed to meet specific performance criteria.
3. Consumer Goods
Consumer products ranging from kitchenware to toys are increasingly produced using thermoforming. The ability to design complex shapes and intricate details makes it an ideal process for designers aiming to enhance usability and aesthetic appeal.
4. Medical Devices
The medical industry relies on precision-made components for devices and packaging. Thermoforming provides the capability to meet stringent regulatory requirements while delivering custom designs that ensure product safety and efficacy.
The Role of Technology in Thermoforming Mold Design
As industries advance, so does the technology involved in thermoforming mold design. The evolution of 3D printing has revolutionized this field, enabling rapid prototyping of molds that were once time-consuming and costly to produce. Here’s how technology impacts thermoforming:
1. Rapid Prototyping
3D printing allows designers to create and test molds quickly, facilitating innovation. This rapid prototyping process enables businesses to iterate designs swiftly, ensuring that final products meet user demands accurately.
2. Customization
Modern thermoforming systems can accept customized mold designs, enhancing the producer’s ability to deliver tailored solutions for specific applications. This level of customization has become a significant market differentiator.
3. Simulation and Optimization
Software tools that simulate the thermoforming process aid designers in optimizing mold designs before physical production. This proactive approach reduces the likelihood of design flaws, leading to increased efficiency and reduced costs.
Challenges in Thermoforming Mold Design and Solutions
While thermoforming mold design offers numerous advantages, it does present challenges as well. Addressing these must be a priority for manufacturers aiming for quality and efficiency.
1. Material Limitations
Different polymers exhibit varying thermal properties, which can impact the design and functionality of the mold. Choosing the right material is essential to achieving desired results.
2. Design Complexity
Complex designs may pose difficulties during the manufacturing process. Utilizing advanced design software and technologies can help streamline the production of intricate mold shapes.
3. Cost Management
Even with optimized processes, challenges remain in keeping costs down. Businesses need to evaluate their supply chains, production techniques, and material choices to ensure sustainability without compromising quality.
The Future of Thermoforming Mold Design
As industries continue to evolve, the future of thermoforming mold design looks promising. Here are some trends that are likely to shape the landscape:
- Sustainability: There is a growing demand for eco-friendly materials and processes in the manufacturing sector. Thermoforming is uniquely positioned to adapt to these requirements, allowing for the use of recyclable materials and minimizing waste.
- Intelligent Manufacturing: The integration of IoT and AI technologies in manufacturing processes is on the rise. These technologies enable smart thermforming machines that can monitor performance in real time and adjust operations for optimal results.
- Global Collaboration: As markets become more interconnected, companies can leverage expertise and resources around the globe, leading to innovation in thermoforming technologies and practices.
Conclusion
In summary, thermoforming mold design is a crucial aspect of modern product development, impacting various industries and applications. Its ability to produce high-quality, custom components quickly and cost-effectively makes it an invaluable tool in the arsenal of manufacturers. By embracing technological advancements and addressing challenges head-on, businesses like arti90.com can continue to lead the way in innovative product design and development. As we look to the future, sustaining and enhancing the versatility of thermoforming processes will undoubtedly play a key role in providing solutions that meet the changing needs of consumers and industries alike.